
Each of these can have several causes (Table 1). Excessive and/or unnecessary deviations from set point can result from oscillations, sluggish control loop response, and excessive measurement noise. Poor control performance makes itself evident primarily when a controlled variable (process variable) deviates excessively from its target value (set point).

Tuners can spend many hours trying to tune these challenging control loops, but the loops often remain problematic. These loops may oscillate for seemingly no reason or deviate far from their set points during load ramps and disturbances, often overshooting their set points afterward.
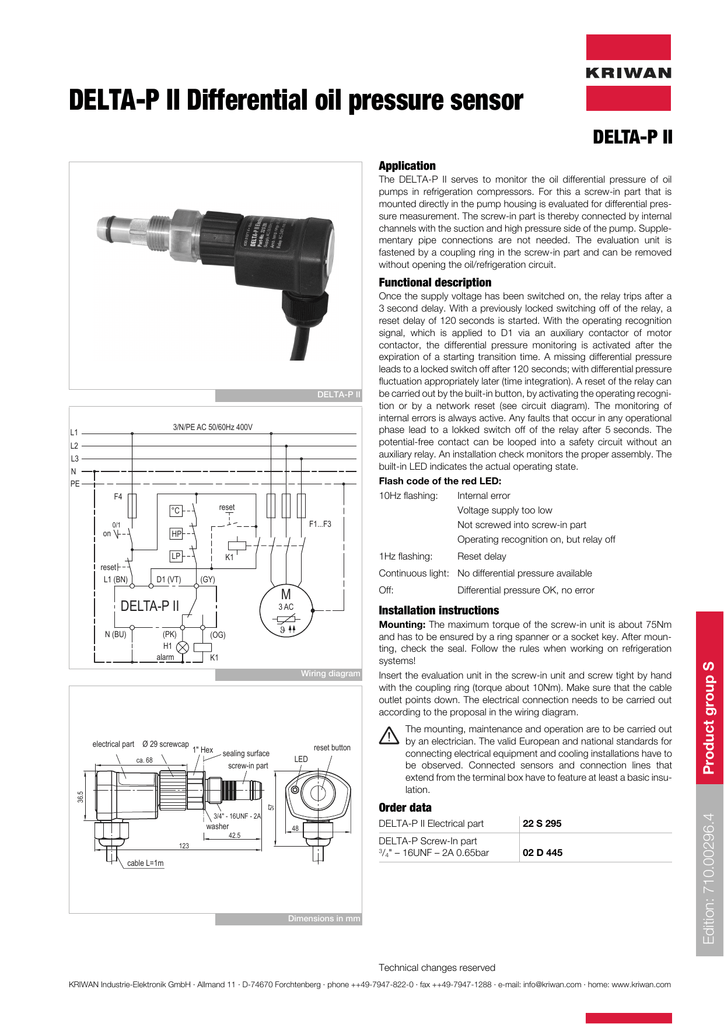
Most power plants have a few control loops that never seem to control satisfactorily. Process design certainly plays a role in control loop performance, but experience has shown that the majority of control loops can perform better-provided that the root cause of the poor performance is found and corrected. The magnitudes of the three terms (P, I and D) are adjusted by the dials at the top.Only through proper troubleshooting and then solving the underlying problems can control loop performance be improved. But the PID controller is broadly applicable since it relies only on the response of the measured process variable, not on knowledge or a model of the underlying process. The response of the controller can be described in terms of its responsiveness to an error, the degree to which the system overshoots a setpoint, and the degree of any system oscillation. In these cases lead–lag compensation is required to be effective. Situations may occur where there are excessive delays: the measurement of the process value is delayed, or the control action does not apply quickly enough. The use of the PID algorithm does not guarantee optimal control of the system or its control stability (see § Limitations, below). PI controllers are fairly common in applications where derivative action would be sensitive to measurement noise, but the integral term is often needed for the system to reach its target value. This is achieved by setting the unused parameters to zero and is called a PI, PD, P or I controller in the absence of the other control actions. A PID controller continuously calculates an error value e ( t ) Selective use of control terms Īlthough a PID controller has three control terms, some applications need only one or two terms to provide appropriate control.
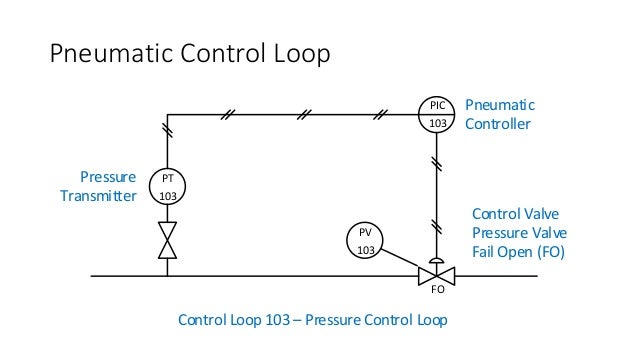
A proportional–integral–derivative controller ( PID controller or three-term controller) is a control loop mechanism employing feedback that is widely used in industrial control systems and a variety of other applications requiring continuously modulated control.
